Brick Inlay crosses the Pacific delivering New Zealand’s first full brick façade – Part 2
- Belinda Findlay
- Mar 28, 2021
- 4 min read
Updated: Feb 8, 2023

Cooper and Co and Bracewell Construction were initially nervous about using Brick Inlay in New Zealand, given the risk of bricks detaching in a seismic event. So they needed considerable convincing to get them across the line, and provided full support in the research process.
The first step was proving Brick Inlay’s solid history. Discussions with Peter Robertson, Director, Robertson Façade Systems, put their fears to bed given Brick Inlay’s proven performance in the key earthquakes zones of Los Angeles and San Francisco. A strong first tick.
The next, more telling, step would be the deal breaker: Six months of rigorous compliance testing.
Cheshire Architects, Mott MacDonald and Holmes Solutions worked together, with Robertson’s Façade Systems and Wilson Group, to produce a series of mock-up brick panels that were rigorously tested to prove the building could withstand New Zealand’s earthquake requirements (which are more stringent since the Christchurch earthquake). There were smaller scale pull-out tests and large scale mock-ups, including one large panel created by Holmes Solutions that represented all of the difficult conditions that the architects would have with their facade such as corners, windows and heavy reinforced sections.

The results were positive and helped the team refine the hotel’s construction.
The design concept was to have a monolithic structure that is the external skin, with the brick on top, which also carries the load through the building. However testing showed that by stitching all of the panels together you end up with a ridged tube sitting on columns underneath. A definite no-no in an earthquake.
“In a seismic event, you don’t want the weakest part of your building to be at the base. So the north and south facades were stitched together as sheer walls, which was great because this meant it didn’t look like a panelised building. Then a steel structure was used behind the east and west architectural panels (so called because they were much less reinforced at 150mm instead of 250mm). This allows for the twisting movement through the building in a seismic event, which stops it pulling itself off its column at the base,” explains Tom Webster, Architect, Cheshire Architects.
This process of testing and refinement though lengthy, reaped rewards:
“The process was a little bit worrying until it was completed, but we knew we had a robust system. And Peter Robertson was so great to work with, plus they have all of the architectural bricks that you could ever want–and we were really attracted to those–and the fact that you could put the Krause bricks we chose in the Brick Inlay system that Peter could warranty, and was practical in the time we had, seemed really good to us,” continues Tom.
Cheshire Architects couldn’t be happier: “We’re really pleased with the way it turned out in terms of the panels – you don’t necessarily see where the panels are in the building, and that was really helped by the variability of colour in the Krause bricks. You read it as a single object with lots of texture and pattern and interest in it, and definitely not as an individual panel,” Tom remarks.

To emphasise the monolithic structure, the building cantilevers out beyond the glass podium and Krause bricks wrap underneath the facade in a soffit. This is the first thing you see at street level, so it was important to get it right. Tom worked with Peter Robertson and Holmes Solutions to test four different conditions of brick that were placed onto the soffit – hung on high beams, stuck to the concrete beam behind or placed on anchor pins bonded into the bricks.
“The placement of those bricks and how they all fit together and how they’re arranged was something we spent a lot of time getting right. It’s one of those architectural details that if you got it wrong, you’d see it. Peter was really helpful; Robertson’s were much more willing than some companies you come across to get in and help us to prototype and generally help us along with that process,” Tom concludes.

There’s no doubt teamwork made all the difference to The Hotel Britomart. The determination and persistence of the team, combined with the flexibility and robust capabilities of Brick Inlay, enabled Cheshire Architects to realise its spectacular design.
And the result is jaw-droppingly good.
Excitingly for Robertson Façade Systems, it’s the first time Brick Inlay has been used in New Zealand. “Our team was thrilled to be involved in such a challenging and rewarding project and, in particular, to work with Cheshire Architects’ Dajiang Tai and Tom Webster to help them achieve their vision. It’s wonderful to see Brick Inlay used in New Zealand, and we look forward to being able to work with Cheshire Architects again,” says Peter.
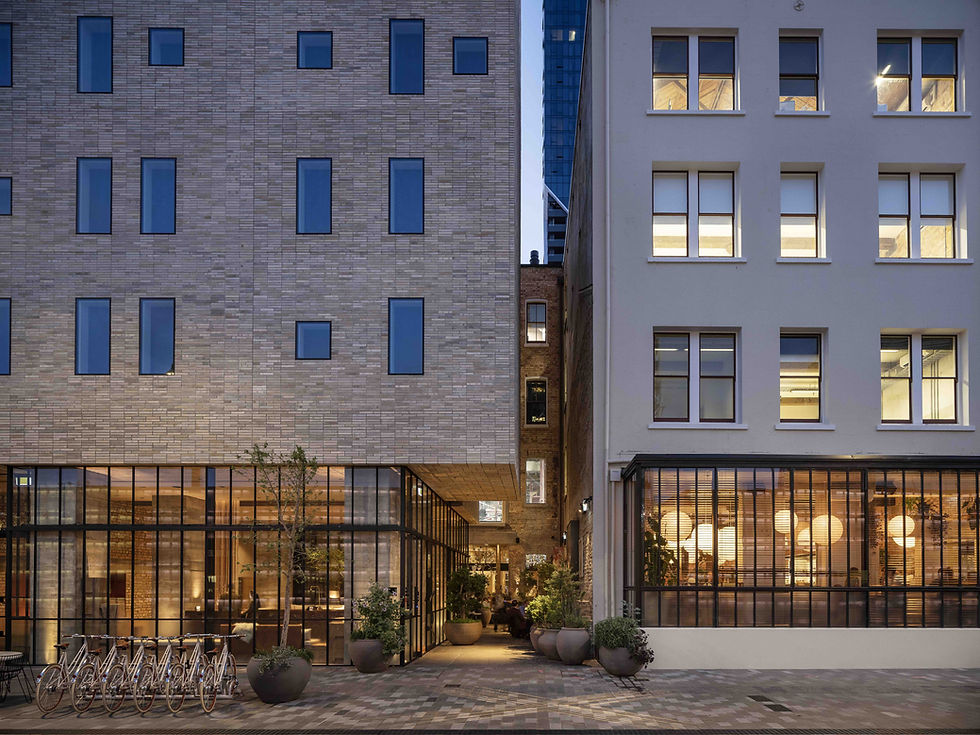
Perhaps Peter won’t be waiting too long, as Dajiang concludes, “Brick Inlay is a very maturely developed system. We needed a system to make our design work, and we wanted to use Robertson’s bricks. It all worked really well, and we’d definitely use Brick Inlay again.”
Stay tuned for the final blog in our three part series on The Hotel Britomart to hear how the custom material palette created a standout project in the Auckland CBD skyline.
Developer: Cooper & Co
Architect: Cheshire Architects
Product: Brick Inlay with custom slimline Krause Grey brick tile blend
Builder: Bracewell Construction
Interior Design: Cheshire Architects, in collaboration with Lukas Design on Suites
Engineers: Mott MacDonald
Precaster: Wilson Group
Photographer: Sam Hartnett Petra Leary (aerials)
Comments